Lesezeit 7 Minuten
Auf einen Blick
Geräte und Anlagen neueren Datums verfügen standardmäßig über eine Vielzahl von Sensoren, die jede Menge Daten erfassen. Auch alte Maschinen lassen sich problemlos mit Sensorik nachrüsten („Retrofit“). Diese können Sie unter anderem nutzen, um frühzeitig Probleme Ihrer Anlagen zu erkennen und ungeplante Ausfälle zu vermeiden. Mit der Methode der vorausschauenden Instandhaltung (engl. Predictive Maintenance) laufen Ihre Maschinen zuverlässiger und sind besser verfügbar. Energieintensive Neustarts sind deutlich seltener nötig. Alles in allem kann die Energieeffizienz in Bezug auf die gewünschte Maschinenleistung (Stück/Ergebnis pro Zeiteinheit) erheblich verbessert werden.
Nutzen Sie Ihre fortlaufenden Daten über den Zustand Ihrer Maschinen bzw. Ihrer gesamten Fertigung und setzen Sie sie kostensenkend ein: durch Optimierung Ihrer Instandhaltung mit Predictive Maintenance!
Mehr Energieeffizienz durch datengestützte Analysemodelle
Deutschland will bis 2045 treibhausgasneutral werden. Der Industrie kommt dabei eine Schlüsselrolle zu. Digitale Lösungen und datengestützte Ansätze bieten hier eine vielversprechende Möglichkeit. Maschinen, die nicht optimal arbeiten, verbrauchen oft mehr Energie als notwendig. Beispielsweise kann ein erhöhter Verschleiß eines Motors zu einem höheren Energieverbrauch führen.
Mit datengestützten Analysemodellen (KI) lassen sich solche Effizienzverluste frühzeitig erkennen. Sensoren und KI-Modelle analysieren den Energieverbrauch der Maschinen und identifizieren Abweichungen vom Normalzustand. Unternehmen können so gezielt eingreifen und Energieverluste minimieren. Dies spart Kosten und erhöht die Nachhaltigkeit der Produktion.
Durch digitale Lösungen und datengestützte Analysemodelle lassen sich Einsparpotenziale von bis zu 20 Prozent zu realisieren.
So funktioniert Predictive Maintenance
Mit der vorausschauenden Instandhaltung (engl. Predictive Maintenance) werden zielgerichtet alle Maschinen- und Prozessdaten erfasst und verarbeitet. Mit geeigneten Analysen und speziellen Algorithmen werden sogenannte datengestützte Analysemodelle entwickelt. Die folgenden Schritte sind dabei maßgeblich:
- Daten sammeln: Sensoren an der Maschine messen verschiedene Werte wie Temperatur, Vibration, Druck oder Stromverbrauch.
- Daten analysieren: Die gesammelten Daten werden von einer Software und Künstlicher Intelligenz (KI) ausgewertet. Dabei wird festgestellt, ob es Anzeichen für Probleme gibt.
- Vorhersagen treffen: Mit Hilfe von Algorithmen wird berechnet, wann ein Bauteil wahrscheinlich ausfällt. So weiß man, wann eine Wartung notwendig ist.
- Handeln: Basierend auf den Vorhersagen kann die Maschine gezielt gewartet werden – bevor ein Defekt auftritt.
Voraussetzungen für den Einsatz datengestützter Analysemodelle
Damit datengestützte Analysemodelle bei der Wartung von Maschinen erfolgreich eingesetzt werden können, brauchen Unternehmen zunächst eine gute Datenbasis. Das bedeutet:
- Informationen, die von Sensoren und anderen Geräten gesammelt werden, müssen präzise, vollständig und aktuell sein, sodass sie verlässliche Analysen ermöglichen.
- Mit Standardisierter Datenübertragung können Anlagen untereinander vernetzt werden und einheitlich kommunizieren
- Die Quelle der Daten muss vertrauenswürdig sein.
- Die Daten müssen konsistent, leicht zugänglich sowie relevant für den jeweiligen Zweck sein.
- Bei der Erhebung und Speicherung muss der Datenschutz beachtet werden.
Für Erhebung, Speicherung und Aufbereitung ist eine gute technische Ausstattung sowie geschultes Personal notwendig:
- Fachpersonal: Expertinnen und Experten sind notwendig, um die Ergebnisse zu interpretieren und geeignete Maßnahmen abzuleiten.
- Sensoren und IoT-Geräte: Maschinen müssen mit Sensoren ausgestattet sein, die relevante Daten wie Temperatur, Druck oder Vibration erfassen.
- Analysesoftware: Analysemodelle müssen implementiert werden, um die Daten sinnvoll auszuwerten.
- Dateninfrastruktur: Eine leistungsfähige Infrastruktur zur Speicherung, Verarbeitung und Übertragung der Daten ist entscheidend.
Robuste Dateninfrastruktur als Basis der Datenverarbeitung im Unternehmen
Um Predictive Maintenance umzusetzen, muss zunächst die Frage geklärt werden, wo die gesammelten Daten verarbeitet werden sollen. Hier kommen zwei Ansätze ins Spiel: Edge Computing und Cloud Computing. Beide Ansätze bieten Vor- und Nachteile, je nach Anwendungsfall und Anforderungen. Doch wie unterscheiden sie sich, und welcher Ansatz ist für Predictive Maintenance am besten geeignet?
Cloud-Computing ermöglicht es, große Datenmengen zentral zu speichern und komplexe Analysen durchzuführen, während Edge-Computing Daten direkt am Ort ihrer Entstehung, also direkt "am Rand" (engl. edge) des Netzwerks, verarbeitet. Dadurch können Unternehmen schneller auf kritische Wartungsbedarfe reagieren, ohne dass alle Daten erst in die Cloud übertragen werden müssen. Auch die in die Cloud zu übertragende Datenmenge lässt sich so reduzieren.
Die Kombination dieser Technologien erlaubt es, sowohl zeitkritische Entscheidungen lokal zu treffen als auch langfristige Analysen in der Cloud durchzuführen, was die Effizienz und Genauigkeit der vorausschauenden Wartung weiter verbessert. Genügend Computerleistung ist wichtig, damit die datengestützten Analysemodelle die Daten schnell verarbeiten können.
Zusätzlich müssen Fachleute vorhanden sein, die diese Daten analysieren und datengestützte Analysemodelle einsetzen können. Führungskräfte des Unternehmens sollten den Einsatz von KI unterstützen und eine entsprechende Unternehmenskultur fördern. Schließlich müssen Sicherheits- und Datenschutzmaßnahmen getroffen werden, um die gesammelten Daten zu schützen und Verstößen gegen die datenschutzrechtlichen Vorgaben vorzubeugen.
Die Kosten können sich deutlich unterscheiden: Cloud Computing ist mit (Anbieter-)Zusatzkosten verbunden, während Edge Computing womöglich günstiger sein kann.
Einen vertiefenden Einblick in das Thema gibt es bei: ComputerWeekly.
Einführung von KI zur vorausschauenden Instandhaltung – ein Wegweiser für KMU
Um KI-Modelle zur vorausschauenden Instandhaltung einzusetzen, ist es unverzichtbar Ihre Mitarbeitenden entsprechend zu schulen. Sie sollten verstehen, warum es wichtig ist, die Maschinen vorab zu warten.
- Beginnen Sie damit, Ihre wichtigsten Maschinen und Geräte zu identifizieren.
- Installieren Sie geeignete Sensoren an den Maschinen, damit Sie Echtzeitdaten sammeln können.
- Sammeln Sie auch ältere Daten über die Maschinen, zum Beispiel frühere Messwerte und Wartungsprotokolle, und bereinigen Sie diese Daten.
- Identifizieren Sie die Arten von Fehlern, die bei Ihren Maschinen auftreten können, und legen Sie fest, wann eine Wartung notwendig ist.
- Achten Sie darauf, dass Ihre Daten sicher sind und der Datenschutz nicht verletzt wird.
- Wählen Sie ein passendes KI-Modell aus, um Ihre Maschinen zu überwachen. Trainieren Sie dieses Modell mit den gesammelten Daten, damit es lernt, Muster und Probleme zu erkennen.
- Sorgen Sie dafür, dass die Sensoren ständig neue Daten an das KI-Modell senden. Richten Sie ein Benachrichtigungssystem ein, das Ihre Mitarbeiter informiert, wenn ein Problem erkannt wird.
- Überprüfen Sie dann diese Daten auf ungewöhnliche Muster.
- Erstellen Sie einen Wartungsplan basierend auf den Erkenntnissen der KI und planen Sie die notwendigen Wartungsarbeiten.
- Überwachen Sie regelmäßig die Leistung des KI-Systems und passen Sie das Modell bei Bedarf an, um es zu verbessern. Führen Sie Aufzeichnungen über alle Wartungsaktivitäten und nutzen Sie diese Informationen, um das KI-System kontinuierlich zu optimieren.
Mit diesem Vorgehen stellen Sie sicher, dass Ihre Maschinen effizient und zuverlässig arbeiten, Ausfallzeiten reduziert werden und Sie Kosten und Energie sparen.
Weiterführende Literatur zur Künstlichen Intelligenz
Das könnte auch interessant sein
Energiedatenmanagement
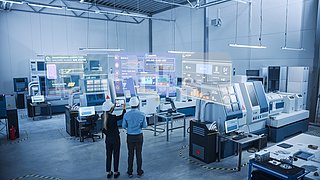
Ein Energiemanagementsystem unterstützt, Effizienzpotenziale zu identifizieren und zu heben. Auf unserer Themenseite erläutern wir alles rund um Aufbau, Umsetzung und Fördermöglichkeiten.
Standardisierte Datenübertragung
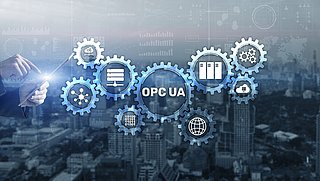
Die automatisierte und standardisierte Datenübertragung zwischen Maschinen und Anlagen ist unabdingbar für die Digitalisierung. Dafür braucht es einheitliche Kommunikationsprotokolle. Wir erklären Ihnen die Vorteile des Kommunikationsframeworks OPC UA.
Förderwegweiser
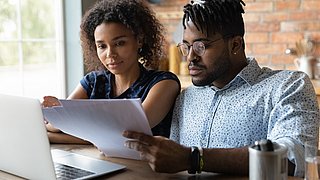
Eine Übersicht an Förderprogrammen, die speziell Digitalisierungsmaßnahmen in Unternehmen unterstützen.
Ihre Ansprechpersonen
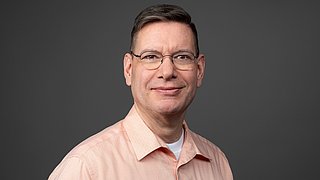
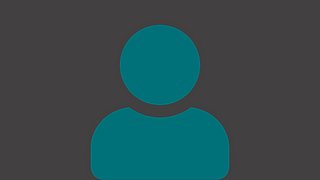